Use of technology to improve supply chain article explores the transformative impact of technological advancements on modern supply chain management. From real-time tracking and predictive analytics to automation and blockchain, this article delves into the diverse applications reshaping efficiency, transparency, and resilience across various industries. We’ll examine how businesses leverage these tools to overcome challenges, optimize operations, and ultimately achieve a significant return on investment.
The integration of technology is no longer a luxury but a necessity for businesses aiming for competitiveness in today’s dynamic market. This article will illuminate how strategic technology adoption can streamline processes, enhance decision-making, and foster stronger collaborations within the supply chain ecosystem. We will explore specific technologies, analyze their impact, and offer practical insights for businesses seeking to modernize their operations.
Introduction
The integration of technology into supply chains is no longer a futuristic concept but a critical necessity for businesses striving for competitiveness and resilience in today’s dynamic global market. While adoption rates vary significantly across industries, a clear trend emerges: businesses are increasingly leveraging technology to optimize their supply chain operations, from procurement to delivery. Mature industries like manufacturing and logistics have seen more widespread adoption, often utilizing sophisticated systems for inventory management and transportation optimization. However, even traditionally less tech-focused sectors are beginning to embrace digital solutions, driven by the need for improved efficiency and transparency.
Current State of Supply Chain Technology Adoption
The current state of supply chain technology adoption reveals a spectrum of maturity levels across different industries. While some sectors, such as logistics and manufacturing, have embraced advanced technologies like AI and blockchain, others, such as retail and agriculture, are still in the earlier stages of digital transformation. This disparity is influenced by factors such as the industry’s inherent complexity, the availability of suitable technologies, and the financial resources available for investment. For instance, large multinational corporations often have the resources to invest in sophisticated systems like Enterprise Resource Planning (ERP) software, while smaller businesses might rely on simpler solutions or individual applications. The adoption rate is also accelerating due to increased pressure to improve efficiency, reduce costs, and enhance customer satisfaction. This acceleration is further fueled by the growing availability of affordable and user-friendly technologies.
Three Key Supply Chain Challenges Addressed by Technology
Businesses face numerous challenges in managing their supply chains. Three key areas where technology offers significant improvement are: inventory management, real-time visibility, and risk mitigation. Inefficient inventory management leads to stockouts or excess inventory, both of which are costly. Technology, such as RFID tracking and demand forecasting algorithms, can optimize stock levels, minimizing waste and maximizing availability. Lack of real-time visibility into the supply chain creates uncertainty and delays. Solutions like GPS tracking and blockchain technology provide complete transparency, allowing businesses to monitor goods in transit and respond quickly to disruptions. Finally, unforeseen events like natural disasters or geopolitical instability can severely disrupt supply chains. Technology can help mitigate these risks through predictive analytics and contingency planning, enabling proactive responses to potential problems.
Potential Return on Investment (ROI) of Supply Chain Technology, Use of technology to improve supply chain article
Implementing technology solutions to improve supply chain efficiency can yield substantial returns on investment. These returns manifest in several ways, including reduced operational costs, improved inventory management, faster delivery times, and enhanced customer satisfaction. For example, a company that implements a warehouse management system (WMS) might experience a significant reduction in labor costs and inventory shrinkage. Similarly, a company that uses predictive analytics to optimize its transportation routes can reduce fuel consumption and transportation costs. The ROI can be quantified by comparing the costs of implementing the technology with the resulting savings in operational expenses, increased sales, and reduced risks. While the initial investment can be significant, the long-term benefits often outweigh the upfront costs, making it a worthwhile endeavor for businesses seeking sustainable growth and improved profitability. A well-executed implementation can result in a significant increase in efficiency and a noticeable reduction in overall operational costs. This often translates to increased profitability and a stronger competitive advantage in the marketplace.
Real-time Visibility and Tracking
Real-time visibility and tracking within the supply chain represent a significant leap forward in efficiency and responsiveness. By leveraging technology to monitor goods throughout their journey, businesses gain unprecedented control, minimizing disruptions and optimizing operations. This enhanced visibility translates directly into improved inventory management, reduced costs, and increased customer satisfaction.
Real-time tracking systems fundamentally alter inventory management by providing accurate, up-to-the-minute data on product location and status. This eliminates the reliance on estimations and outdated information, allowing for more precise forecasting and demand planning. Consequently, stockouts, a common source of lost revenue and customer frustration, are significantly reduced. The ability to pinpoint exactly where goods are at any given moment enables proactive adjustments to inventory levels, preventing overstocking or shortages.
RFID, GPS, and Blockchain Technologies in Tracking
Several technologies contribute to real-time tracking, each with its own strengths and weaknesses. Radio-Frequency Identification (RFID) tags, small electronic devices attached to products, transmit unique identification codes that can be read by scanners at various points in the supply chain. Global Positioning System (GPS) technology utilizes satellites to track the precise location of goods, particularly beneficial for shipments in transit. Blockchain technology, a decentralized and secure ledger, provides an immutable record of a product’s journey, enhancing transparency and traceability.
RFID excels in high-volume tracking environments, efficiently monitoring numerous items simultaneously. However, its accuracy can be affected by obstacles and its range is limited. GPS provides highly accurate location data, ideal for tracking shipments across long distances. However, it’s less effective for tracking individual items within a warehouse or distribution center. Blockchain offers unparalleled security and transparency, but its implementation can be complex and expensive. The optimal choice often involves a combination of these technologies, leveraging the strengths of each to create a comprehensive tracking system.
Preventing Supply Chain Disruptions with Real-Time Visibility
Imagine a scenario involving a major automotive manufacturer. They are experiencing a critical shortage of a specific microchip, a crucial component for their flagship vehicle model. Without real-time tracking, identifying the location and status of the delayed shipment would be a lengthy and complex process, potentially resulting in significant production delays and financial losses.
However, with a comprehensive real-time tracking system in place, the manufacturer immediately identifies the shipment’s location – currently stalled due to unexpected port congestion. Using this information, they proactively reroute the shipment via air freight, incurring additional costs but avoiding a far greater production shutdown. The real-time visibility provided by the tracking system allows for rapid decision-making, minimizing the impact of the disruption and ensuring continued production. This illustrates the significant value of real-time visibility in mitigating risks and maintaining operational continuity within the supply chain.
Predictive Analytics and Forecasting
Predictive analytics leverages historical data, statistical algorithms, and machine learning techniques to forecast future outcomes. In the context of supply chain management, this translates to more accurate demand forecasting, optimized inventory levels, and ultimately, reduced costs and improved efficiency. By analyzing past sales data, market trends, and external factors, businesses can gain valuable insights into future demand patterns, enabling proactive adjustments to their supply chain strategies.
Predictive analytics empowers businesses to move beyond reactive responses to demand fluctuations and instead anticipate and prepare for future needs. This proactive approach minimizes stockouts, reduces waste from excess inventory, and enhances overall supply chain responsiveness. The ability to accurately predict demand is crucial for optimizing procurement, production, and distribution processes.
Machine Learning Algorithms Enhance Forecasting Accuracy
Machine learning algorithms significantly improve the accuracy of supply chain forecasting by identifying complex patterns and relationships within large datasets that traditional methods often miss. These algorithms can handle various data types, including time series data, categorical data, and external factors like economic indicators or weather patterns. For instance, a recurrent neural network (RNN) can effectively model the temporal dependencies in sales data, leading to more accurate short-term and long-term forecasts. Similarly, support vector machines (SVM) can identify non-linear relationships between variables, improving the overall accuracy of the prediction model. The use of these sophisticated algorithms allows for a more nuanced understanding of demand drivers, leading to better-informed decisions.
Utilizing Historical Data to Create a Robust Predictive Model for a Specific Product
Let’s consider a hypothetical example: a company manufacturing and distributing seasonal clothing, specifically winter coats. Using historical sales data from the past five years, encompassing sales figures for each month, regional variations, weather data for those periods, and marketing campaign effectiveness, a predictive model can be built. This data would be cleaned and pre-processed to handle missing values and outliers. Features like month, year, average temperature, precipitation, and marketing spend could be used as input variables to predict future demand. A machine learning algorithm, such as a gradient boosting machine (GBM), could be trained on this data to learn the relationship between these input features and the sales of winter coats. The model would then be validated using a separate dataset to assess its accuracy before deployment. This allows the company to accurately forecast demand for the upcoming winter season, optimizing inventory levels to minimize excess stock and avoid stockouts, thereby maximizing profitability. The model can also be refined and updated regularly by incorporating new data and adjusting for unforeseen events or changing market conditions. This iterative process ensures the model remains accurate and effective over time.
Automation and Robotics in Warehousing and Logistics
The integration of automation and robotics is revolutionizing warehousing and logistics, significantly impacting efficiency, speed, and cost-effectiveness. This transformation involves the deployment of various technologies designed to streamline operations, from receiving and storage to order fulfillment and shipping. The adoption of these technologies varies depending on factors such as warehouse size, product type, and budget, but the overall trend points towards increased automation across the industry.
Robots are increasingly common in warehouses, performing tasks previously handled manually. This automation boosts productivity and reduces operational costs. Different types of robots cater to specific needs, each contributing to improved warehouse efficiency. The choice of robots depends on the specific requirements of the warehouse and the types of goods being handled.
Types of Robots Used in Warehouses and Their Impact on Efficiency
Several types of robots are employed in modern warehouses, each designed for specific tasks. Automated Guided Vehicles (AGVs) navigate the warehouse floor, transporting goods between different areas. Articulated robots, with multiple joints and axes of movement, are often used for tasks such as picking and packing. Collaborative robots, or “cobots,” work alongside human workers, assisting with tasks that require both human dexterity and robotic precision. Autonomous mobile robots (AMRs) offer more sophisticated navigation capabilities than AGVs, adapting to dynamic warehouse environments. Finally, conveyor systems, while not strictly robots, are integral to automated warehousing, transporting items along predefined routes. The deployment of these robots results in faster order fulfillment, reduced errors, and improved overall warehouse throughput.
Cost and Benefit Analysis of Automating Warehouse Operations
The decision to automate warehouse operations involves a careful cost-benefit analysis. While initial investment costs for robots and automation systems can be substantial, the long-term benefits often outweigh the expenses. Automation leads to reduced labor costs, lower error rates, and increased efficiency, ultimately boosting profitability. However, factors such as the size of the warehouse, the complexity of operations, and the type of goods handled influence the overall cost-effectiveness of automation. For example, a large e-commerce warehouse handling a high volume of small items might find automation particularly beneficial, while a smaller warehouse with a limited product range might find manual processes more cost-effective.
Automated Guided Vehicle (AGV) Capabilities and Limitations
Automated Guided Vehicles (AGVs) are a key component of automated warehousing. Different types of AGVs exist, each with unique capabilities and limitations. The following table compares several common AGV types:
AGV Type | Navigation Method | Payload Capacity | Limitations |
---|---|---|---|
Wire-guided AGV | Follows embedded wires in the floor | Varies, typically up to several tons | Limited flexibility, difficult to reconfigure routes |
Magnetic-tape guided AGV | Follows magnetic tape embedded in the floor | Varies, typically up to several tons | Similar limitations to wire-guided AGVs |
Laser-guided AGV | Uses lasers to navigate based on pre-programmed maps | Varies, typically up to several tons | Requires accurate mapping, can be affected by obstacles |
Vision-guided AGV | Uses cameras and computer vision to navigate | Varies, depending on the model | More complex and expensive, requires sophisticated software |
Supply Chain Collaboration and Communication
Effective communication and collaboration are paramount to a smoothly functioning supply chain. Technology plays a crucial role in fostering these vital elements, enabling real-time information sharing, enhanced transparency, and stronger relationships between all stakeholders. This leads to improved efficiency, reduced costs, and increased responsiveness to market demands.
Improved data sharing and collaborative platforms are transforming how supply chain partners interact. By breaking down information silos and providing a single source of truth, these technologies build trust and foster a more proactive approach to problem-solving and opportunity identification. This section will explore the benefits of these technological advancements.
Benefits of Collaborative Platforms
Collaborative platforms offer a centralized hub for communication and data sharing among all supply chain participants, from manufacturers and suppliers to distributors and retailers. This centralized approach eliminates the delays and inaccuracies inherent in traditional methods like email and phone calls. The benefits include faster response times to disruptions, improved coordination of activities, and the ability to proactively address potential issues before they escalate. For instance, a platform might allow a retailer to immediately notify a supplier of a sudden surge in demand, allowing the supplier to adjust production accordingly, preventing stockouts and lost sales. This proactive approach is a significant improvement over relying on lagging indicators or infrequent communication.
Enhanced Transparency and Trust Through Data Sharing
Real-time data sharing is a cornerstone of improved trust and transparency. When all stakeholders have access to the same accurate, up-to-date information, uncertainty is reduced, and collaborative problem-solving becomes easier. For example, if a shipment is delayed, all parties are immediately aware, allowing them to collaboratively find solutions, such as rerouting or finding alternative transportation. This open communication builds trust and strengthens relationships. The shared visibility minimizes the potential for misunderstandings and finger-pointing, fostering a more collaborative and efficient environment. Furthermore, the ability to track key performance indicators (KPIs) across the entire supply chain allows for objective assessment of performance and identification of areas for improvement.
Examples of Successful Collaborations
Several companies have successfully leveraged technology to enhance supply chain collaboration. For example, Walmart uses its Retail Link system to share real-time sales data with its suppliers. This allows suppliers to optimize their production and inventory levels, leading to reduced costs and improved responsiveness to demand. Similarly, many companies in the automotive industry utilize collaborative platforms to manage the complex supply chains involved in vehicle production. These platforms facilitate communication and coordination between various suppliers, ensuring timely delivery of parts and minimizing disruptions. The result is improved efficiency, reduced lead times, and a more resilient supply chain. These examples demonstrate how technology can transform traditionally siloed operations into highly collaborative and efficient systems.
Inventory Optimization and Management
Effective inventory management is crucial for a successful supply chain. Optimizing inventory levels directly impacts profitability by minimizing storage costs, preventing stockouts, and ensuring timely order fulfillment. Technology plays a pivotal role in achieving this optimization, offering real-time insights and predictive capabilities that were previously unavailable.
Inventory management software provides a centralized platform for tracking inventory levels across multiple locations, automating order processing, and generating accurate forecasts. This reduces manual errors, improves data accuracy, and streamlines operations. By providing a clear picture of inventory levels and demand patterns, businesses can make informed decisions about purchasing, production, and warehousing, leading to significant reductions in holding costs – the expenses associated with storing and maintaining inventory. Simultaneously, optimized inventory management enhances order fulfillment by minimizing stockouts and ensuring that products are available when and where they are needed. This directly translates to improved customer satisfaction and increased sales.
Key Metrics for Evaluating Inventory Management System Effectiveness
Three key metrics provide a comprehensive evaluation of an inventory management system’s performance. These metrics offer quantifiable insights into efficiency and areas for improvement.
- Inventory Turnover Rate: This metric measures how many times a company’s inventory is sold and replaced over a specific period (usually a year). A higher turnover rate generally indicates efficient inventory management and strong sales. For example, a turnover rate of 6 means that the entire inventory was sold and replaced six times during the year. A low turnover rate might suggest overstocking or slow-moving inventory. The formula for calculating inventory turnover rate is: Cost of Goods Sold / Average Inventory.
- Inventory Holding Costs: This represents the total cost associated with storing and maintaining inventory, including warehousing costs, insurance, taxes, obsolescence, and spoilage. A lower holding cost percentage (as a percentage of total inventory value) indicates efficient inventory management. For example, a company aiming for a 15% holding cost would strive to keep these costs at or below 15% of their total inventory value. Analyzing these costs allows for identifying areas of potential savings, such as negotiating better warehousing rates or implementing improved storage strategies.
- Fill Rate: This metric measures the percentage of customer orders fulfilled from available inventory. A high fill rate indicates efficient inventory management and strong customer service. For example, a 95% fill rate means that 95% of customer orders were fulfilled immediately from stock. A low fill rate might indicate stockouts, leading to lost sales and customer dissatisfaction. Improving the fill rate requires accurate demand forecasting and efficient inventory replenishment strategies.
Best Practices for Inventory Optimization Across Product Categories
Effective inventory optimization requires a tailored approach based on the specific characteristics of different product categories. Implementing these best practices can significantly improve inventory management across the board.
- ABC Analysis: Categorize inventory into A, B, and C items based on their value and consumption. Focus more attention and resources on managing A items (high value, high consumption) and less on C items (low value, low consumption). This prioritization allows for more effective resource allocation.
- Demand Forecasting: Employ sophisticated forecasting techniques, such as time series analysis and machine learning, to predict future demand accurately. This enables proactive inventory management and reduces the risk of stockouts or overstocking. For example, a retailer might use historical sales data and external factors (like seasonality or economic trends) to predict demand for winter coats during the upcoming fall season.
- Safety Stock Management: Determine appropriate safety stock levels for each product category to account for unexpected demand fluctuations or supply chain disruptions. This ensures continuous supply and minimizes the risk of stockouts. The optimal safety stock level is a balance between minimizing holding costs and avoiding stockouts. For example, a company selling perishable goods might hold higher safety stock to account for potential spoilage.
Transportation and Logistics Optimization: Use Of Technology To Improve Supply Chain Article
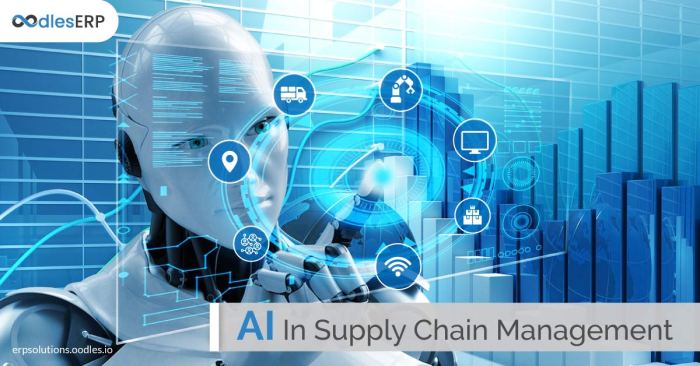
Optimizing transportation and logistics is crucial for efficient supply chain management. Reducing transportation costs and delivery times directly impacts profitability and customer satisfaction. Effective strategies involve leveraging technology to improve route planning, select the most suitable transportation mode, and enhance fleet management.
Route optimization software analyzes various factors such as distance, traffic patterns, delivery deadlines, and fuel costs to determine the most efficient routes for shipments. This significantly reduces transportation expenses by minimizing fuel consumption and driver downtime. Faster delivery times also enhance customer satisfaction and improve overall operational efficiency.
Route Optimization Software Impacts
Route optimization software utilizes sophisticated algorithms to consider numerous variables and dynamically adjust routes based on real-time data. For example, a delivery company using such software might see a 15% reduction in fuel costs and a 10% decrease in delivery times compared to traditional methods relying on manual route planning. This translates to substantial savings and improved on-time delivery performance. The software’s ability to account for unforeseen events like traffic congestion or road closures ensures that deliveries remain on schedule, even amidst unexpected circumstances.
Transportation Mode Comparison
Selecting the appropriate transportation mode is critical for balancing cost, speed, and environmental impact. Each mode offers unique advantages and disadvantages.
Transportation Mode | Cost | Speed | Environmental Impact |
---|---|---|---|
Truck | Moderate | Moderate | Moderate |
Rail | Low | Slow | Low |
Air | High | Fast | High |
Sea | Low | Slow | Low |
For example, transporting large quantities of goods over long distances is often more cost-effective via rail or sea, despite the slower transit times. Air freight, while expensive, is ideal for time-sensitive shipments of smaller, high-value goods. Trucking provides flexibility for last-mile delivery and reaches areas inaccessible to other modes. The environmental impact varies significantly, with air freight having the highest carbon footprint and rail and sea transportation generally being the most environmentally friendly. The choice depends on a careful consideration of these factors in relation to specific supply chain needs.
GPS Tracking and Telematics in Fleet Management
GPS tracking and telematics systems provide real-time visibility into fleet operations. These systems track vehicle location, speed, mileage, and driver behavior, providing valuable data for optimizing routes, reducing fuel consumption, and improving driver safety.
GPS tracking allows for proactive management of deliveries, enabling dispatchers to monitor vehicle progress and adjust schedules as needed. Telematics data, including driver speed and idling time, can be used to identify areas for improvement in driver training and fuel efficiency. For instance, identifying drivers consistently exceeding speed limits allows for targeted training to improve fuel economy and reduce accident risk. Similarly, data on idling time highlights areas where operational procedures can be improved to reduce fuel waste. The integration of this data allows for data-driven decision-making, leading to significant improvements in fleet efficiency and cost reduction.
Cybersecurity and Data Protection in the Supply Chain
The increasing reliance on technology within supply chains has unfortunately introduced new vulnerabilities to cyberattacks and data breaches. These attacks can disrupt operations, damage reputations, and lead to significant financial losses. Protecting sensitive data and ensuring the security of supply chain systems is therefore paramount for maintaining business continuity and customer trust. This section will explore the key aspects of cybersecurity and data protection within the modern supply chain.
Supply chains are complex ecosystems involving numerous interconnected parties, systems, and data flows. This interconnectedness creates a large attack surface, making them attractive targets for malicious actors. Vulnerabilities can exist at any point in the chain, from suppliers and manufacturers to distributors, retailers, and even consumers. Potential threats include ransomware attacks that cripple operations, data breaches exposing sensitive customer information, and supply chain manipulation through compromised systems. The consequences can range from minor operational disruptions to catastrophic financial losses and irreversible reputational damage.
Best Practices for Supply Chain Data Security
Implementing robust cybersecurity measures is crucial to mitigate these risks. A multi-layered approach is recommended, combining technological safeguards with strong operational practices. This involves regular security assessments to identify vulnerabilities, employee training programs to promote cybersecurity awareness, and the implementation of strong access controls to limit unauthorized access to sensitive data. Furthermore, robust data encryption protocols are essential to protect data both in transit and at rest. The use of multi-factor authentication (MFA) adds an extra layer of security, making it significantly harder for unauthorized individuals to gain access to systems. Finally, regular backups and disaster recovery planning are vital to ensure business continuity in the event of a cyberattack.
Regulatory Compliance Requirements for Supply Chain Data Security
Several regulations mandate specific data security measures for businesses handling sensitive information within their supply chains. Compliance with these regulations is not merely a matter of avoiding penalties; it’s a demonstration of a commitment to responsible data handling and customer trust. For example, the General Data Protection Regulation (GDPR) in Europe imposes stringent requirements on the processing of personal data, impacting companies globally. Similarly, the California Consumer Privacy Act (CCPA) in the United States grants consumers greater control over their personal information. Other relevant regulations include the Payment Card Industry Data Security Standard (PCI DSS) for companies handling credit card information and industry-specific regulations related to healthcare data (HIPAA) or financial data (SOX). Understanding and adhering to these regulations is vital for businesses operating in the global supply chain.
Mitigating Risks Through Technology and Collaboration
Technology plays a vital role in enhancing supply chain cybersecurity. This includes the use of blockchain technology for enhanced traceability and transparency, reducing the risk of counterfeiting and fraud. Implementing intrusion detection and prevention systems can provide early warnings of suspicious activities. Regular security audits and penetration testing help identify and address vulnerabilities before they can be exploited. Moreover, fostering strong collaboration and information sharing among supply chain partners is crucial. This allows for the rapid identification and response to threats, limiting the potential impact of incidents. A collaborative approach ensures that everyone understands their responsibilities in maintaining the security of the shared ecosystem.
The Internet of Things (IoT) in Supply Chain Management
The Internet of Things (IoT) is revolutionizing supply chain management by providing unprecedented levels of real-time visibility and data-driven insights. Through the deployment of interconnected sensors and devices, businesses gain a granular understanding of their operations, leading to improved efficiency, reduced costs, and enhanced customer satisfaction. This enhanced visibility allows for proactive decision-making, optimizing various aspects of the supply chain from procurement to delivery.
IoT sensors and devices embedded within products, packaging, and transportation assets generate a continuous stream of data regarding product location, condition, and environmental factors. This data is then transmitted wirelessly to a central system for analysis and action. For example, temperature sensors on refrigerated trucks ensure perishable goods remain within optimal temperature ranges, while GPS trackers provide real-time location information, enabling efficient route planning and proactive response to potential delays. This constant stream of information offers a level of control and understanding previously unattainable.
IoT Data Enhances Predictive Maintenance and Reduces Equipment Downtime
Predictive maintenance, driven by IoT data analytics, significantly reduces equipment downtime and associated costs. By analyzing sensor data from machinery and equipment, businesses can identify potential issues before they escalate into major failures. For example, vibration sensors on a conveyor belt can detect subtle changes indicative of impending wear and tear, allowing for timely maintenance and preventing costly production halts. This proactive approach minimizes unexpected disruptions and extends the lifespan of equipment, ultimately contributing to substantial cost savings. Companies using predictive maintenance strategies based on IoT data often report significant reductions in maintenance costs and improved operational uptime. A study by Gartner predicted that by 2025, 80% of enterprise-grade IoT projects will include predictive maintenance capabilities.
Hypothetical IoT-Enabled Supply Chain System for Pharmaceutical Products
Consider a pharmaceutical company distributing temperature-sensitive medications. An IoT-enabled system would incorporate several key components: Firstly, temperature and humidity sensors within each shipping container monitor conditions throughout the entire journey. Secondly, GPS trackers provide real-time location information, allowing for efficient route optimization and immediate notification of any delays. Thirdly, RFID tags on individual drug packages allow for granular tracking and verification of product authenticity and integrity. Data from all these sources is transmitted wirelessly to a central cloud-based platform, providing a complete, real-time view of the supply chain. This system enables proactive alerts for temperature excursions, potential delays, or counterfeiting attempts, ensuring product quality and patient safety. The benefits include minimized product loss due to spoilage, reduced operational costs through optimized logistics, and improved regulatory compliance by providing complete audit trails. The system also allows for enhanced supply chain resilience by enabling quick identification and mitigation of disruptions.
Blockchain Technology for Enhanced Transparency and Traceability
Blockchain technology offers a revolutionary approach to supply chain management by providing an immutable, transparent, and secure record of product movement and provenance. This distributed ledger technology enhances traceability, combats counterfeiting, and improves overall efficiency throughout the entire supply chain.
Blockchain’s impact on product traceability stems from its decentralized and encrypted nature. Each transaction or event in the supply chain—from raw material sourcing to final delivery—is recorded as a “block” on the blockchain. This creates a chronological, auditable trail that can be accessed by authorized parties, offering unparalleled visibility into the product’s journey. Unlike traditional databases, which are centralized and vulnerable to manipulation, blockchain’s distributed structure makes it extremely resistant to tampering.
Blockchain’s Role in Verifying Product Authenticity and Preventing Counterfeiting
The inherent security and transparency of blockchain are powerful tools in the fight against counterfeiting. By recording unique product identifiers and related certifications on the blockchain, manufacturers can create a verifiable digital identity for each item. Consumers and businesses can then scan a product’s unique code to confirm its authenticity, ensuring they are purchasing genuine goods. This verification process is nearly impossible to bypass, as any attempt to alter the blockchain record would be immediately detected by the network. For example, a luxury goods company could use blockchain to track each handbag from its creation to the point of sale, providing consumers with irrefutable proof of authenticity and discouraging the sale of counterfeit products. This transparency not only protects consumers but also safeguards brand reputation and revenue for legitimate businesses.
Comparison of Blockchain and Traditional Databases for Supply Chain Data Management
Traditional databases, while useful for many applications, fall short when it comes to the demanding requirements of transparent and secure supply chain data management. They are centralized, meaning a single point of failure exists, and data can be easily altered or deleted. Access control is often complex and requires significant trust in the database administrator. Blockchain, conversely, offers a decentralized, immutable ledger. Data is distributed across multiple nodes, making it highly resistant to single points of failure and manipulation. Access control is managed through cryptographic keys, ensuring only authorized parties can view or modify data. While traditional databases are optimized for speed and efficient querying of structured data, blockchain excels in providing verifiable, tamper-proof records, prioritizing data integrity over speed. This difference is crucial in supply chain management where trust and accountability are paramount. For instance, a food producer using a traditional database might face difficulties in tracing a contaminated batch back to its source due to potential data inaccuracies or manipulation. With blockchain, the complete history of the batch would be readily available and immutable, facilitating rapid identification and resolution of the problem.
Emerging Technologies and Future Trends
The rapid pace of technological advancement continues to reshape the landscape of supply chain management. While technologies like AI and blockchain are already making an impact, several emerging trends promise even more significant transformations in the next five to ten years. These advancements offer the potential to enhance efficiency, resilience, and sustainability across the entire supply chain ecosystem. Understanding and strategically implementing these technologies will be crucial for businesses seeking a competitive edge in the increasingly complex global marketplace.
Three Emerging Technologies with Transformative Potential
Three key technologies poised to revolutionize supply chain management in the coming years are extended reality (XR), digital twins, and quantum computing. These technologies, while still in relatively early stages of adoption, offer unique capabilities to optimize various aspects of the supply chain, from design and planning to execution and monitoring.
- Extended Reality (XR): Encompassing virtual reality (VR), augmented reality (AR), and mixed reality (MR), XR technologies offer immersive training simulations for warehouse workers, enabling them to practice complex tasks in a safe and controlled environment. AR can overlay digital information onto the real world, guiding technicians during equipment maintenance or allowing warehouse staff to locate items more efficiently. This results in reduced training times, improved accuracy, and increased worker safety.
- Digital Twins: A digital twin is a virtual representation of a physical asset or process. In supply chain management, this could be a digital twin of a warehouse, a transportation network, or even an entire supply chain. These digital replicas allow for real-time monitoring, simulation of various scenarios (e.g., disruptions, demand fluctuations), and optimization of processes before implementation in the real world. For instance, a company could use a digital twin to test the impact of a new warehouse layout on efficiency before making costly physical changes.
- Quantum Computing: While still in its nascent stages, quantum computing has the potential to solve complex optimization problems far beyond the capabilities of classical computers. This could revolutionize route optimization, demand forecasting, and inventory management by enabling the analysis of significantly larger datasets and more intricate scenarios. For example, quantum algorithms could find the most efficient routes for a fleet of delivery trucks considering real-time traffic conditions, significantly reducing delivery times and fuel consumption.
Artificial Intelligence and Machine Learning in Supply Chain Optimization
Artificial intelligence (AI) and machine learning (ML) are already impacting supply chain optimization, and their influence will only grow stronger. AI and ML algorithms can analyze vast amounts of data from various sources (e.g., sales data, weather patterns, sensor readings) to identify patterns, predict future trends, and automate decision-making processes.
This translates to improved demand forecasting, optimized inventory levels, more efficient route planning, and proactive risk management. For instance, ML algorithms can analyze historical sales data and weather patterns to predict demand for specific products in different regions, allowing businesses to adjust their inventory levels accordingly and prevent stockouts or overstocking. AI-powered systems can also monitor real-time data from sensors on trucks and in warehouses to detect potential problems (e.g., equipment malfunctions, delays) and trigger appropriate actions before they escalate into major disruptions.
Challenges and Opportunities in Adopting New Technologies
The adoption of these emerging technologies presents both challenges and opportunities. Significant upfront investments in infrastructure, software, and training are required. Furthermore, integrating new technologies with existing systems can be complex and time-consuming. Data security and privacy concerns are also paramount, as these technologies often rely on the collection and analysis of sensitive data.
However, the potential benefits far outweigh the challenges. By embracing these technologies, businesses can gain a significant competitive advantage by improving efficiency, reducing costs, enhancing resilience, and increasing customer satisfaction. The successful implementation of these technologies requires a strategic approach, a commitment to ongoing learning and adaptation, and a focus on building robust data security and governance frameworks. Companies that proactively address these challenges will be well-positioned to reap the rewards of these transformative technologies.
Summary
In conclusion, the strategic implementation of technology offers a powerful pathway to optimize and future-proof supply chains. By embracing real-time visibility, predictive analytics, automation, and enhanced collaboration, businesses can significantly improve efficiency, reduce costs, and enhance resilience against disruptions. As technology continues to evolve, staying informed and adaptable will be crucial for maintaining a competitive edge in the ever-changing landscape of global supply chain management. The journey towards a more efficient and robust supply chain is a continuous process of innovation and adaptation, and the technologies discussed here represent key milestones in that journey.