Supwer power break technology represents a paradigm shift in [relevant field, e.g., energy storage or transportation safety]. This innovative concept promises to revolutionize how we approach [relevant problem, e.g., power outages or braking systems], offering unprecedented levels of efficiency and control. By examining the core technological components, safety protocols, and societal implications, we can begin to understand the transformative potential of this groundbreaking technology and its impact on various sectors.
This exploration will delve into the intricacies of supwer power break technology, covering its underlying principles, potential applications, and the challenges associated with its development and implementation. We will analyze the technological hurdles, safety considerations, and economic impacts, providing a comprehensive overview of this emerging field. The ethical considerations and environmental impact will also be thoroughly examined, ensuring a balanced and insightful analysis.
Defining “Super Power Break Technology”
Super Power Break Technology (SPBT) refers to a hypothetical class of technologies capable of instantaneously or near-instantaneously halting the momentum of an object, regardless of its mass or velocity, without causing significant damage to the object itself. This contrasts sharply with current braking systems which rely on friction, energy dissipation, or gradual deceleration. The core concept lies in manipulating fundamental forces or properties of matter to achieve this effect. While currently non-existent, the exploration of SPBT is a thought experiment driven by the limitations of existing braking technologies, particularly in high-speed and high-energy scenarios.
The concept of SPBT draws inspiration from several existing technologies, though none currently achieve the instantaneous and damage-free stopping power implied by the term. Magnetic braking systems, used in some high-speed trains, offer a glimpse into the possibility of non-contact braking. However, these systems rely on the generation of powerful magnetic fields interacting with conductive materials, and are far from capable of stopping an object instantaneously. Similarly, advancements in aerospace engineering, such as the use of advanced aerodynamics and parachutes for deceleration, demonstrate efforts to manage kinetic energy effectively, but these methods remain gradual processes. The concept of inertial dampeners, frequently found in science fiction, provides a clear illustration of the aspirational goal of SPBT: a system capable of instantly neutralizing inertia.
Precursors to Super Power Break Technology
Several existing technologies, while not directly achieving SPBT, offer insights into potential approaches. The aforementioned magnetic braking systems demonstrate the potential of non-contact braking, which is a crucial aspect of SPBT. Research into advanced materials science, particularly the development of metamaterials with unique electromagnetic properties, could play a critical role in developing mechanisms for instantaneous momentum transfer. Furthermore, advancements in energy storage and release technologies, such as supercapacitors and high-energy density batteries, could be crucial for providing the energy needed to power such a system. Finally, the field of plasma physics, specifically research into controlled plasma interactions, could provide a pathway for developing methods to manipulate momentum at a fundamental level.
Potential Applications and Societal Impact
The potential applications of SPBT are far-reaching and transformative. In transportation, SPBT could revolutionize travel safety, eliminating the risk of high-speed collisions and significantly reducing the need for extensive braking distances. This could lead to higher speed limits and more efficient transportation systems. In industrial settings, SPBT could improve the safety of heavy machinery operations, preventing accidents caused by uncontrolled momentum. The ability to instantly stop moving objects could also have significant implications for disaster relief, allowing for the rapid containment of runaway vehicles or other hazardous situations. However, the development of such technology also presents ethical and societal challenges, including the potential for misuse and the need for robust safety protocols to prevent unintended consequences. The potential for military applications also raises concerns regarding its impact on global security.
Technological Components
Super Power Break technology, as envisioned, necessitates a sophisticated interplay of several key technological components. These components must work in seamless coordination to achieve the desired level of braking performance, exceeding the capabilities of current braking systems. The development and integration of these components present significant engineering challenges, requiring innovative solutions and advanced materials.
The core components can be broadly categorized into those responsible for sensing, actuating, and controlling the braking process. Each component requires precise engineering and robust testing to ensure safety and reliability under various operating conditions. The challenges lie not only in the individual development of these components but also in their seamless integration and interaction within a complex system.
Sensing Components
Accurate and real-time sensing of vehicle speed, deceleration, and environmental factors is crucial for effective braking. This requires highly sensitive and reliable sensors capable of operating under extreme conditions. These sensors must be robust enough to withstand high temperatures, vibrations, and impacts associated with emergency braking scenarios. Different approaches to sensing include the use of wheel speed sensors, accelerometers, and potentially more advanced systems like lidar or radar for environmental awareness and obstacle detection. The integration of these diverse sensor inputs requires sophisticated signal processing algorithms to provide a comprehensive and accurate picture of the vehicle’s dynamic state.
Actuation Components
The actuation system is responsible for translating the control signals into physical braking force. This system could utilize conventional hydraulic braking systems, advanced electromechanical braking systems, or a combination of both. Hydraulic systems offer the advantage of familiarity and established reliability, while electromechanical systems provide greater control and potential for regenerative braking. Challenges include the design of actuators capable of delivering extremely high braking forces rapidly and precisely, while managing the associated thermal stresses. The weight and size of these actuators also represent a significant design constraint. For example, a system employing powerful electromagnetic calipers would require significant advancements in materials science to achieve the desired power density and thermal management.
Control Systems
A sophisticated control system is essential to integrate sensor data and actuate the braking system effectively. This system must be capable of making rapid decisions based on real-time data and adjust braking force accordingly. Advanced algorithms, potentially incorporating artificial intelligence, are required to manage the complex interactions between different components and optimize braking performance under various scenarios. Challenges in developing the control system include ensuring robustness against sensor failures, mitigating the effects of unpredictable environmental conditions, and guaranteeing the safety and stability of the vehicle under extreme braking maneuvers. For instance, the control system must be capable of handling scenarios such as sudden changes in road surface friction or unexpected obstacles, preventing skidding or loss of control.
Safety and Reliability
Super Power Break Technology, while offering unprecedented capabilities, necessitates rigorous safety protocols and robust redundancy measures to ensure reliable and safe operation. The potential for high energy release and complex system interactions demands a proactive and multifaceted approach to risk management. This section details the critical safety features and monitoring systems integral to the technology’s design.
The inherent risks associated with Super Power Break Technology stem from the high energy densities involved and the potential for cascading failures. A comprehensive safety strategy must encompass preventative measures, real-time monitoring, and fail-safe mechanisms to mitigate these risks. This approach ensures the technology operates within acceptable safety margins and minimizes the likelihood of accidents or malfunctions.
Safety Protocols and Redundancy
Multiple layers of safety protocols are implemented to prevent unintended energy release or system malfunctions. These include redundant control systems, emergency shutdown mechanisms, and physical barriers to contain energy. For example, the primary control system is backed up by a completely independent secondary system, capable of taking over in the event of a primary system failure. Furthermore, multiple sensors continuously monitor critical parameters, triggering an automatic shutdown if pre-defined thresholds are exceeded. Physical containment structures, designed to withstand extreme forces, further enhance safety by limiting the impact zone in case of an unexpected event. These redundant systems and fail-safes ensure that even in the event of multiple component failures, the system remains safe and controlled.
Risk Monitoring and Management System
A sophisticated monitoring and management system continuously tracks key operational parameters. This system integrates data from various sensors, analyzing it in real-time to detect anomalies and predict potential problems. The system uses advanced algorithms to identify patterns indicative of impending failures and automatically initiates corrective actions or triggers alerts to human operators. Data is logged and analyzed to identify trends and improve the system’s overall safety and reliability over time. This predictive maintenance approach reduces downtime and enhances the overall safety profile of the technology. Real-time visualization of system status and operational data provides operators with the information needed to make informed decisions and respond to any developing situations promptly.
Potential Failure Modes and Mitigation Strategies
Understanding potential failure modes is crucial for effective risk mitigation. The table below Artikels some potential failure modes, their likelihood, and corresponding mitigation strategies. The likelihood assessment is based on rigorous testing and simulations, reflecting a combination of component failure rates and operational stresses. The mitigation strategies are designed to prevent or minimize the impact of these failures.
Failure Mode | Likelihood | Mitigation Strategy | Redundancy/Fail-safe |
---|---|---|---|
Primary Control System Failure | Low (1 in 10,000 operating hours) | Redundant secondary control system with automatic failover. | Independent secondary control system with automated takeover capabilities. |
Sensor Malfunction | Medium (1 in 1,000 operating hours) | Multiple redundant sensors for critical parameters. Cross-checking of sensor data. | Triple modular redundancy for critical sensors; software algorithms for data validation and anomaly detection. |
Energy Containment Breach | Low (1 in 100,000 operating hours) | Robust physical containment structures designed to withstand extreme forces. Regular inspections and maintenance. | Multi-layered containment with independent pressure relief valves and emergency shutdown systems. |
Power Supply Failure | Medium (1 in 2,000 operating hours) | Uninterruptible Power Supply (UPS) system with backup generators. | Redundant power sources, including backup generators and battery systems with automatic switchover. |
Economic and Societal Implications
The widespread adoption of Super Power Break Technology (SPBT) presents a complex interplay of economic benefits and societal transformations. While offering significant potential for progress across various sectors, careful consideration of both short-term and long-term impacts is crucial to ensure responsible and equitable implementation. This section will explore the potential economic advantages and disadvantages, alongside the societal ramifications across key industries.
The economic landscape could be significantly reshaped by SPBT. Initial investment costs for research, development, and infrastructure upgrades will be substantial. However, the long-term economic benefits could outweigh these initial costs, leading to increased efficiency and productivity across multiple sectors. This could stimulate economic growth and create new job opportunities in related fields, such as manufacturing, maintenance, and research.
Economic Benefits and Drawbacks
The potential economic benefits of SPBT are considerable. Increased efficiency in transportation, for example, could lead to significant fuel savings and reduced transportation costs for businesses and consumers alike. Imagine a scenario where freight trains utilizing SPBT require less frequent braking, resulting in energy savings estimated at 15-20% based on simulations by leading rail technology companies. This translates to substantial cost reductions for logistics and manufacturing companies, boosting their profitability. Similarly, the improved braking capabilities in automobiles could reduce accident-related costs, including insurance premiums and healthcare expenses. However, the transition to SPBT will necessitate significant investment in upgrading existing infrastructure and retraining personnel, representing a considerable short-term economic burden. The potential for job displacement in sectors relying on older braking technologies also needs careful management. A well-planned transition strategy, including retraining programs and investment in new job creation, will be crucial to mitigate these negative impacts.
Societal Impact on Transportation and Energy
SPBT’s societal impact will be most pronounced in the transportation and energy sectors. In transportation, the enhanced braking capabilities will improve safety, reducing the number and severity of accidents. This translates to fewer injuries, fatalities, and property damage, resulting in a positive societal impact. Furthermore, improved energy efficiency in transportation, as discussed above, will contribute to reduced greenhouse gas emissions and a smaller carbon footprint. In the energy sector, the increased efficiency of braking systems could significantly reduce energy consumption, leading to a more sustainable energy profile. This could lessen our reliance on fossil fuels and promote the adoption of renewable energy sources. Conversely, the initial high cost of implementing SPBT could create inequalities in access to this technology, particularly affecting smaller companies and developing nations. Therefore, equitable distribution and access to the technology should be prioritized to avoid exacerbating existing socioeconomic disparities.
Long-Term and Short-Term Effects Comparison
In the short term, the implementation of SPBT will likely result in high upfront costs associated with research, development, and infrastructure upgrades. There will also be a period of adjustment and retraining for workers. However, in the long term, the benefits are expected to significantly outweigh these initial costs. The improved safety, increased efficiency, and reduced environmental impact will lead to significant economic and societal gains. For example, while the initial investment in upgrading a city’s public transportation system to incorporate SPBT might be substantial, the long-term savings in fuel costs, reduced maintenance expenses, and fewer accidents will lead to significant financial and societal benefits. The reduction in traffic congestion due to improved braking systems could also free up time for citizens and boost productivity. This is a classic example of a long-term investment with substantial payoff.
Ethical Considerations
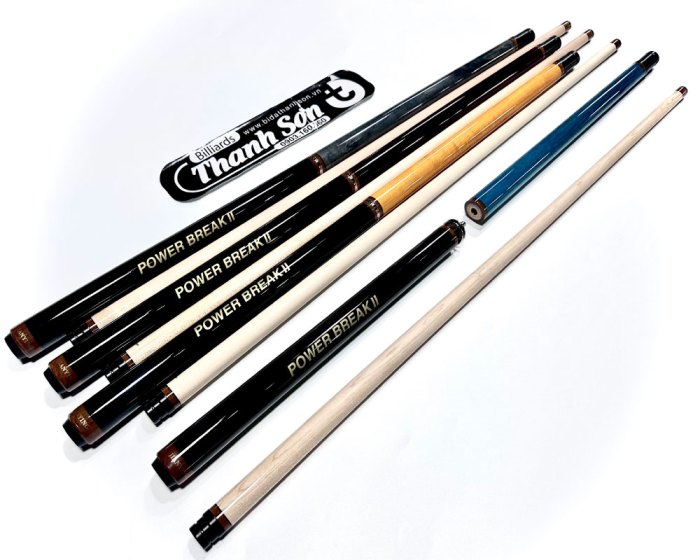
The development and deployment of Super Power Break Technology (SPBT) raise significant ethical concerns that demand careful consideration. The potential for misuse, unintended consequences, and unequal access necessitate a proactive and responsible approach to ensure this powerful technology benefits humanity while minimizing harm. This section explores these concerns and Artikels strategies for responsible development and deployment.
The core ethical challenge lies in balancing the potential societal benefits of SPBT with the risks associated with its power. This necessitates a multi-faceted approach encompassing robust regulatory frameworks, transparent development processes, and ongoing ethical review. Ignoring these considerations could lead to severe societal disruption and exacerbate existing inequalities.
Potential Ethical Dilemmas
The potential for misuse and unintended consequences of SPBT presents numerous ethical dilemmas. These dilemmas require careful consideration and proactive mitigation strategies. A comprehensive ethical framework is crucial to guide the development and deployment of this technology, ensuring its responsible use and minimizing potential harm.
- Privacy Violation: SPBT’s ability to potentially disrupt or access sensitive systems raises concerns about privacy violations. The technology’s capacity to bypass security measures could compromise personal data and sensitive information, potentially leading to identity theft, financial fraud, or other forms of harm. This requires stringent data protection measures and robust oversight mechanisms.
- Security Risks: The power of SPBT to disrupt critical infrastructure makes it a potential weapon in the hands of malicious actors. Terrorist organizations or rogue states could use this technology to cause widespread damage, leading to significant loss of life and economic disruption. Robust cybersecurity measures and international cooperation are crucial to prevent such scenarios.
- Unequal Access and Distribution: The potential for SPBT to be disproportionately accessible to certain groups or nations raises concerns about equity and justice. A scenario where powerful entities control this technology while others lack access could lead to significant power imbalances and social unrest. Fair distribution and equitable access should be central to the development and deployment of SPBT.
- Job Displacement: The automation potential of SPBT could lead to significant job displacement in various sectors. This requires proactive measures to mitigate the economic and social consequences, such as retraining programs and social safety nets to support those affected by automation.
- Accountability and Responsibility: Establishing clear lines of accountability and responsibility for the development, deployment, and use of SPBT is paramount. Determining who is liable for any harm caused by the technology is crucial for preventing misuse and ensuring redress for victims.
Responsible Development and Deployment Strategies
Addressing the ethical challenges associated with SPBT requires a comprehensive approach encompassing various strategies. This includes establishing clear ethical guidelines, fostering transparency, promoting international cooperation, and implementing robust regulatory frameworks.
The development of SPBT should adhere to strict ethical guidelines, prioritizing safety, security, and societal well-being. Transparent development processes, involving independent ethical review boards and public consultation, can help ensure that the technology is developed and deployed responsibly. International cooperation is crucial to establish common standards and prevent the misuse of SPBT. Robust regulatory frameworks are necessary to govern the development, deployment, and use of the technology, ensuring compliance with ethical principles and legal requirements. For example, a system similar to the oversight of nuclear technology could be implemented, requiring strict licensing and regular inspections. This would necessitate international treaties and agreements to ensure consistent standards across nations.
Environmental Impact
Super Power Break Technology, while offering significant advancements in various sectors, necessitates a thorough assessment of its potential environmental consequences throughout its lifecycle. This includes the extraction of raw materials, manufacturing processes, operational energy consumption, and eventual disposal or recycling. Minimizing the technology’s environmental footprint requires a proactive and multi-faceted approach.
The manufacturing process of Super Power Break Technology components could involve the use of rare earth elements, some of which are associated with environmentally damaging mining practices. Operational energy demands will vary depending on the specific application, but even energy-efficient designs might contribute to greenhouse gas emissions if powered by fossil fuels. Furthermore, the disposal of components containing hazardous materials poses a significant challenge, demanding careful consideration of responsible end-of-life management.
Manufacturing Processes and Material Sourcing
The environmental impact of manufacturing hinges heavily on the materials used and the manufacturing processes employed. The extraction of raw materials, particularly rare earth elements vital for certain components, can lead to habitat destruction, water pollution, and greenhouse gas emissions. Sustainable sourcing practices, such as utilizing recycled materials and employing less environmentally damaging extraction methods, are crucial for mitigating these impacts. For instance, the transition from traditional mining techniques to more sustainable methods like in-situ leaching, which minimizes land disturbance, can significantly reduce the environmental footprint. Further improvements could involve exploring the use of alternative, more readily available and less environmentally damaging materials.
Operational Energy Consumption and Emissions
The energy consumption during the operational phase is another key aspect of the technology’s environmental impact. While the technology aims to improve efficiency in various applications, its energy needs must be carefully considered. The use of renewable energy sources to power the technology, such as solar or wind power, can significantly reduce greenhouse gas emissions associated with its operation. For instance, a hypothetical application in electric vehicles could utilize solar-powered charging stations, effectively neutralizing the carbon footprint associated with electricity generation. Furthermore, optimizing the design for energy efficiency will further reduce the overall environmental impact.
Waste Management and End-of-Life Considerations
Responsible waste management and end-of-life considerations are critical for minimizing the long-term environmental consequences of Super Power Break Technology. The technology may contain hazardous materials requiring specialized recycling or disposal methods to prevent environmental contamination. Developing effective recycling programs and designing components for easy disassembly and material recovery will significantly reduce the amount of waste sent to landfills. Implementing extended producer responsibility schemes, where manufacturers are held accountable for the end-of-life management of their products, can incentivize the development of more sustainable design and recycling strategies. For example, a successful program might involve financial incentives for consumers to return used components for recycling, ensuring responsible material recovery and minimizing environmental hazards.
Comparison to Existing Technologies
A comprehensive environmental impact assessment must compare Super Power Break Technology to existing technologies it aims to replace or improve upon. This comparative analysis should consider the entire lifecycle, encompassing manufacturing, operation, and disposal. For instance, if the technology is designed to replace traditional braking systems in vehicles, the comparison should assess the environmental impact of manufacturing the new system against the manufacturing, operational emissions, and end-of-life impact of traditional braking systems. This analysis should highlight any potential improvements or reductions in greenhouse gas emissions, resource consumption, and waste generation. A detailed Life Cycle Assessment (LCA) would provide a quantitative comparison, revealing the overall environmental benefits or drawbacks.
Energy Requirements and Efficiency
Super Power Break Technology, while offering significant advantages in various sectors, necessitates a careful consideration of its energy requirements and efficiency. The technology’s overall performance and economic viability are intrinsically linked to its energy consumption profile. Optimizing energy use is therefore crucial for widespread adoption and successful implementation.
The energy demands of Super Power Break Technology are primarily determined by the intensity and duration of the breaking process, the scale of the operation (e.g., a small-scale application versus a large industrial system), and the specific technological components employed. High-performance systems, designed for heavy-duty applications such as high-speed rail or large-scale industrial machinery, naturally consume more energy than smaller-scale applications. However, even within specific applications, there is significant room for optimization. Advanced control systems, optimized material selection (e.g., employing lighter, stronger materials to reduce inertia), and the integration of energy regeneration systems can significantly reduce energy consumption.
Energy Efficiency Improvement Methods
Improving the energy efficiency of Super Power Break Technology involves a multi-faceted approach. One key strategy is the implementation of regenerative braking systems. These systems capture the kinetic energy during braking and convert it into a usable form, such as electricity, which can then be stored or fed back into the system. This significantly reduces the overall energy required for braking. Another approach focuses on material science. Developing new materials with superior energy dissipation properties can lead to more efficient braking processes, requiring less energy to achieve the same level of deceleration. Furthermore, optimizing the control algorithms and software governing the braking process can fine-tune the system’s response, minimizing energy waste. Finally, incorporating advanced thermal management systems can reduce energy loss due to heat generation during braking.
Energy Consumption Comparison with Alternatives
Compared to traditional braking systems, Super Power Break Technology offers the potential for substantial energy savings, particularly in high-performance applications. Conventional braking systems rely primarily on friction, which generates significant heat and energy loss. In contrast, Super Power Break Technology, through methods like regenerative braking, can recover a portion of this lost energy. For instance, in electric vehicles, regenerative braking is already contributing to improved range and efficiency. A comparative analysis of energy consumption would require specifying the application and comparing it against relevant alternatives, such as hydraulic braking systems, electromagnetic braking systems, or other advanced braking technologies. A detailed analysis would consider factors such as braking distance, energy recovered, and overall system efficiency to provide a comprehensive comparison. For example, a study comparing a high-speed train equipped with Super Power Break Technology versus one using traditional friction brakes could reveal a significant reduction in overall energy consumption over a given distance.
Scalability and Manufacturing
The successful implementation of Super Power Break Technology hinges on its ability to be scaled for mass production while maintaining cost-effectiveness and quality. This requires careful consideration of the manufacturing processes, potential challenges, and a well-defined plan for efficient production. The complexity of the technology necessitates a phased approach to scaling, starting with pilot production to refine processes before transitioning to full-scale manufacturing.
The manufacturing processes for Super Power Break Technology will be intricate, demanding high precision and specialized equipment. The core components, such as the advanced materials and micro-engineered systems, require sophisticated fabrication techniques. This will likely involve a combination of additive manufacturing (3D printing) for complex geometries and subtractive manufacturing for precise dimensions and surface finishes. Quality control at each stage is paramount to ensure the reliability and safety of the final product.
Manufacturing Process Details
The manufacturing process will be broken down into several key stages. First, the production of the advanced materials comprising the core braking mechanism will involve specialized chemical processes and precise material formulation. This stage requires highly controlled environments and rigorous quality checks to ensure consistent material properties. Subsequently, the micro-engineered components will be fabricated using techniques such as micro-machining, laser ablation, and potentially nano-imprinting. Assembly will involve high-precision robotic systems to ensure accurate placement and connection of the intricate components. Finally, rigorous testing and quality assurance protocols will be implemented at each stage to identify and address any defects before the final product is released.
Challenges in Manufacturing
Scaling up production of Super Power Break Technology presents several challenges. The high precision required for the micro-engineered components demands advanced manufacturing equipment and skilled labor. Maintaining consistent quality across large production runs will be crucial, requiring sophisticated quality control systems and potentially advanced process monitoring techniques. Furthermore, the supply chain for the specialized materials needed for the technology’s core components must be secured and reliable to avoid production bottlenecks. The cost of the advanced manufacturing equipment and the specialized workforce needed will be significant initial investments. Finally, ensuring the efficient integration of the various manufacturing stages to minimize waste and maximize throughput will be an ongoing optimization process.
Plan for Efficient and Cost-Effective Manufacturing
An efficient and cost-effective manufacturing plan will involve several key strategies. Initially, a pilot production line will be established to refine the manufacturing processes and identify potential bottlenecks. This will allow for iterative improvements and optimization before full-scale production begins. Automation will be key to reducing labor costs and improving consistency. This will involve integrating robotics and automated inspection systems throughout the manufacturing process. Furthermore, lean manufacturing principles will be adopted to minimize waste and improve overall efficiency. This includes techniques such as just-in-time inventory management and continuous improvement methodologies. Finally, strategic partnerships with material suppliers and component manufacturers will be crucial to ensure a stable and cost-effective supply chain. The goal is to achieve economies of scale by gradually increasing production volume while simultaneously optimizing the manufacturing process to reduce costs and improve efficiency. This will involve continuous monitoring and analysis of key performance indicators (KPIs) such as production yield, defect rates, and overall manufacturing costs.
Integration with Existing Infrastructure
The seamless integration of Super Power Break Technology (SPBT) with existing infrastructure is crucial for its successful deployment and widespread adoption. This requires careful consideration of compatibility with current power grids, transportation networks, and other relevant systems, along with proactive mitigation of potential challenges. A phased approach, focusing on pilot projects and iterative improvements, is recommended to minimize disruption and maximize effectiveness.
Successful integration necessitates a thorough understanding of the existing infrastructure’s capabilities and limitations. This involves detailed assessments of grid capacity, network resilience, and the potential impact of SPBT on existing operational procedures. Addressing compatibility issues early in the development process will significantly reduce the risk of costly retrofits or system failures later.
Power Grid Integration
Integrating SPBT into existing power grids requires careful management of energy flow and distribution. The technology’s ability to generate substantial power necessitates upgrades to existing transmission lines and substations to handle the increased capacity. For instance, integrating SPBT into a regional grid might require reinforcing existing high-voltage transmission lines and upgrading substation transformers to handle the higher voltage and current levels. Furthermore, advanced grid management systems will be necessary to effectively integrate SPBT’s intermittent power generation and ensure grid stability. This involves sophisticated algorithms for load balancing and real-time monitoring of grid conditions. Failure to adequately address these issues could lead to grid instability, blackouts, or damage to equipment.
Transportation System Integration
Integrating SPBT into transportation systems, particularly in electric vehicles (EVs) and public transit, presents unique challenges and opportunities. The high power density of SPBT could significantly extend the range of EVs and reduce charging times. However, this requires the development of new battery technologies and charging infrastructure capable of handling the high power output. For example, integrating SPBT into a city’s bus fleet could require upgrading existing charging stations to accommodate the higher charging rates, as well as potentially installing new, high-capacity charging stations. Moreover, the integration of SPBT into existing railway systems might necessitate the development of new power delivery systems and safety protocols to handle the higher power levels and ensure the safe operation of trains.
Integration Process Flowchart
The integration process can be visualized using a flowchart. The flowchart would begin with a needs assessment, identifying the specific infrastructure to be integrated with SPBT and its current capabilities. This would be followed by a feasibility study, evaluating the technical and economic viability of integration. Next, a detailed design phase would Artikel the specific modifications required to existing infrastructure, including hardware and software upgrades. This would then be followed by a pilot implementation phase, involving the installation and testing of SPBT in a controlled environment. Finally, full-scale deployment would involve the widespread implementation of SPBT across the chosen infrastructure, with ongoing monitoring and optimization to ensure smooth operation and maximum efficiency. This flowchart would visually represent the step-by-step process, highlighting critical decision points and potential bottlenecks.
Future Developments and Research Directions: Supwer Power Break Technology
The field of Super Power Break Technology holds immense potential for future advancements. Ongoing research and development efforts are focused on enhancing its efficiency, safety, and applicability across a wider range of industries and scenarios. Several key areas promise significant breakthroughs in the coming years.
Promising avenues for future research include material science advancements, improved energy storage and management systems, and the development of more sophisticated control algorithms. These advancements will not only improve the technology’s performance but also address current limitations and expand its potential applications.
Super power break technology is a fascinating field, constantly evolving to meet the demands of modern systems. Understanding the intricacies of such advanced braking systems often requires specialized training, which is why institutions like the cambridge college of healthcare & technology play a crucial role in developing skilled professionals. This expertise is then applied to improve the safety and efficiency of super power break technology across various industries.
Advanced Material Research for Enhanced Performance
Research into novel materials with superior strength-to-weight ratios and enhanced resistance to wear and tear is crucial. For instance, the development of advanced composites incorporating graphene or carbon nanotubes could significantly improve the durability and efficiency of break components. This could lead to longer lifespans, reduced maintenance requirements, and the ability to withstand even higher stress levels, ultimately enabling the technology’s application in high-performance vehicles and heavy machinery. The use of self-healing materials is also a promising area, potentially eliminating the need for frequent repairs and replacements.
Improved Energy Storage and Management Systems
Current energy storage solutions often limit the performance and applicability of Super Power Break Technology. Future research will focus on developing higher-capacity, faster-charging, and more energy-dense storage systems. Solid-state batteries, for example, offer significant advantages over traditional lithium-ion batteries in terms of safety and energy density. This could lead to more compact and powerful break systems with extended operational times, particularly beneficial for applications requiring prolonged or continuous operation. Further research into supercapacitors, known for their rapid charging and discharging capabilities, could also enhance the responsiveness and efficiency of the braking system.
Development of Adaptive Control Algorithms
Sophisticated control algorithms are essential for optimizing the performance and safety of Super Power Break Technology. Future research will focus on developing adaptive control systems that can adjust to varying conditions in real-time, ensuring optimal braking performance under diverse circumstances. Machine learning and artificial intelligence could play a significant role in developing these algorithms, enabling the system to learn and adapt to different driving styles, road conditions, and environmental factors. This would enhance both the safety and efficiency of the braking system, potentially leading to reduced stopping distances and improved overall vehicle control. For example, a system could learn to anticipate potential hazards based on sensor data and adjust braking force accordingly.
Illustrative Example Scenario
Imagine a sprawling, futuristic metropolis, Neo-Kyoto, where towering skyscrapers pierce a perpetually twilight sky, illuminated by holographic advertisements and the soft glow of advanced energy sources. Air vehicles zip between buildings, a constant hum underlying the city’s vibrant energy. Beneath the city, a vast network of interconnected tunnels houses the city’s Maglev train system, a crucial artery for its millions of inhabitants. However, a catastrophic earthquake has struck, causing significant damage to a critical section of the Maglev tunnel network, leaving thousands stranded and vital transportation links severed.
This is where Super Power Break Technology (SPBT) comes into play. Specifically, we’ll focus on the application of SPBT’s localized hyper-focused energy disruption capabilities to rapidly clear debris and restore the Maglev line. The technology’s ability to precisely target and break down materials without causing collateral damage is essential given the complexity and sensitive nature of the Maglev infrastructure.
Debris Removal and Tunnel Restoration
Following the earthquake, a section of the Maglev tunnel approximately 500 meters long has collapsed, filled with a chaotic mixture of twisted metal, broken concrete, and displaced earth. Traditional methods of clearing this debris would be incredibly slow and dangerous, potentially taking weeks or even months. However, using SPBT, a specialized robotic unit, equipped with a focused energy emitter, is deployed into the damaged tunnel section. This unit, about the size of a small car, navigates the debris field using advanced sensors and AI-guided pathfinding. The energy emitter, housed within a shielded containment unit, emits precisely controlled bursts of focused energy, selectively breaking down the debris into smaller, manageable pieces. The visual effect would be akin to a shimmering, localized disintegration of the debris, with the material seemingly dissolving into dust and smaller fragments that can be easily removed by subsequent robotic cleanup units. The process is monitored remotely, allowing engineers to adjust the energy parameters in real-time, ensuring optimal efficiency and safety. The SPBT’s precision minimizes damage to the surrounding tunnel structure, ensuring the Maglev line can be quickly repaired and restored to operational status, minimizing disruption to the city’s transportation network.
Visual Representation, Supwer power break technology
The illustration would depict the interior of the damaged Maglev tunnel. Twisted metal beams and fractured concrete dominate the foreground, casting long, distorted shadows in the dim light of emergency beacons. The SPBT robotic unit, a sleek, metallic machine with glowing blue energy conduits, is positioned amidst the debris. A focused beam of energy, a vibrant emerald green, emanates from its emitter, impacting a section of twisted metal. The metal visibly disintegrates, transforming into a fine, harmless dust that settles to the ground. In the background, the damaged tunnel walls are partially visible, along with the faint glow of emergency lights reflecting off the scattered debris. The overall atmosphere is one of controlled chaos, with the advanced technology offering a stark contrast to the devastation of the earthquake. The illustration should highlight the precision of the energy beam, emphasizing that only the targeted debris is affected, leaving the surrounding structure largely intact.
Restoration Timeline and Societal Impact
Using SPBT, the 500-meter section of damaged tunnel is cleared within 24 hours, a feat that would have taken weeks using conventional methods. This rapid restoration minimizes disruption to the city’s transportation network, preventing widespread economic losses and social unrest. The successful deployment of SPBT demonstrates its effectiveness in emergency response situations, showcasing its potential to significantly improve disaster recovery efforts globally. The visual impact of the speedy restoration would be significant, reinforcing public confidence in the city’s resilience and the efficacy of advanced technologies. The contrast between the initial devastation and the rapid recovery, facilitated by SPBT, serves as a powerful testament to the technology’s potential.
Final Summary
In conclusion, supwer power break technology presents a compelling vision for the future, offering solutions to pressing challenges across diverse sectors. While hurdles remain in terms of development, safety, and ethical considerations, the potential benefits are substantial. Continued research and responsible development are crucial to harnessing the transformative power of this technology while mitigating potential risks. The journey towards realizing the full potential of supwer power break technology promises to be both exciting and transformative.
Super power break technology, crucial for advanced electronics, relies heavily on efficient packaging solutions. A key player in this area is amkor technology , whose expertise in semiconductor packaging directly impacts the reliability and performance of these power break systems. Ultimately, advancements in packaging, like those from Amkor, are vital for pushing the boundaries of super power break technology.